Calculating Equipment Costs
When it comes to creating accurate bid proposals and keeping construction projects on track, one of the biggest challenges for contractors is estimating equipment costs. While there are several different ways to calculate equipment costs, there are some considerations to keep in mind when getting the cost of equipment right.
Own Vs. Rent
If you choose to rent equipment on a per-project basis, this should be a fairly straightforward number to include in your bid proposal — it should (theoretically) be the same cost quoted to you by the rental company. Long-term rentals and leases should be calculated as if the equipment is owned (see below). The cost of using equipment that is owned by the contractor should be calculated using numbers like usage and fixed costs and labor.
Here are some basic universal formulas to keep handy:
Owning costs = purchase price of machine + financing + taxes – disposal (resale) price
Operating costs = labor + fuel + maintenance + replacement costs of tires, tracks and other components + overhead
Cost of Equipment
This is probably the most obvious and complicated cost to calculate. Fixed and variable equipment costs are commonly applied to the equipment cost estimations. Fixed costs include the cost to purchase the equipment for the job along with the annual rate of depreciation of the machinery. Variable costs include the maintenance and operating costs for the equipment, and cover line items like fuel and repairs.
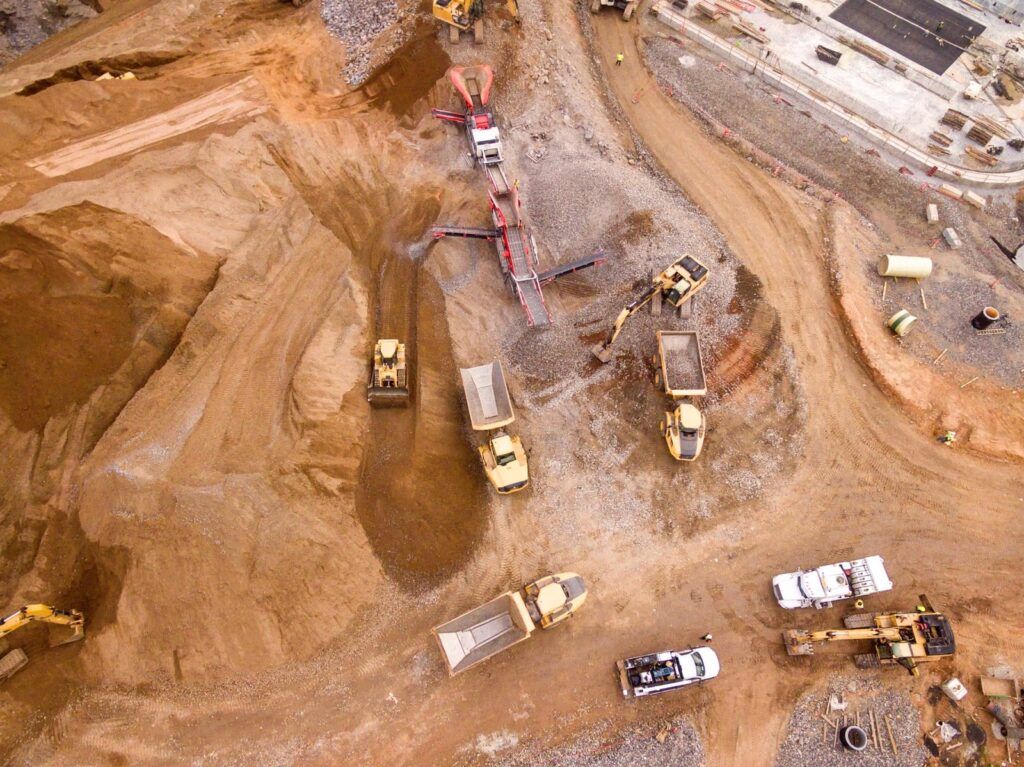
Cost of Preventative Maintenance
This should be a cost calculated independently from any other estimations. Reactive maintenance ultimately costs more and impacts the value greater than preventative maintenance. The equipment cost calculated as part of the bidding process needs to include the cost of training operators to understand maintenance best practices and the price of labor to carry them out.
Cost of Labor
Labor costs are pretty straightforward with the right scheduling and planning strategies in place. Start by calculating the number of hours the equipment will be used, and leverage scheduling software and project planning methodology to calculate the cost of operator labor. Don’t overlook the importance (and cost) of properly training the operators to use the equipment.
The Value of Scheduling and Project Management
It can’t be reiterated enough: The first step to accurately estimating equipment costs for the bidding process is getting a firm grasp of the number of hours that the equipment will be used. This can be best achieved with a focus on project management and construction scheduling best practices.
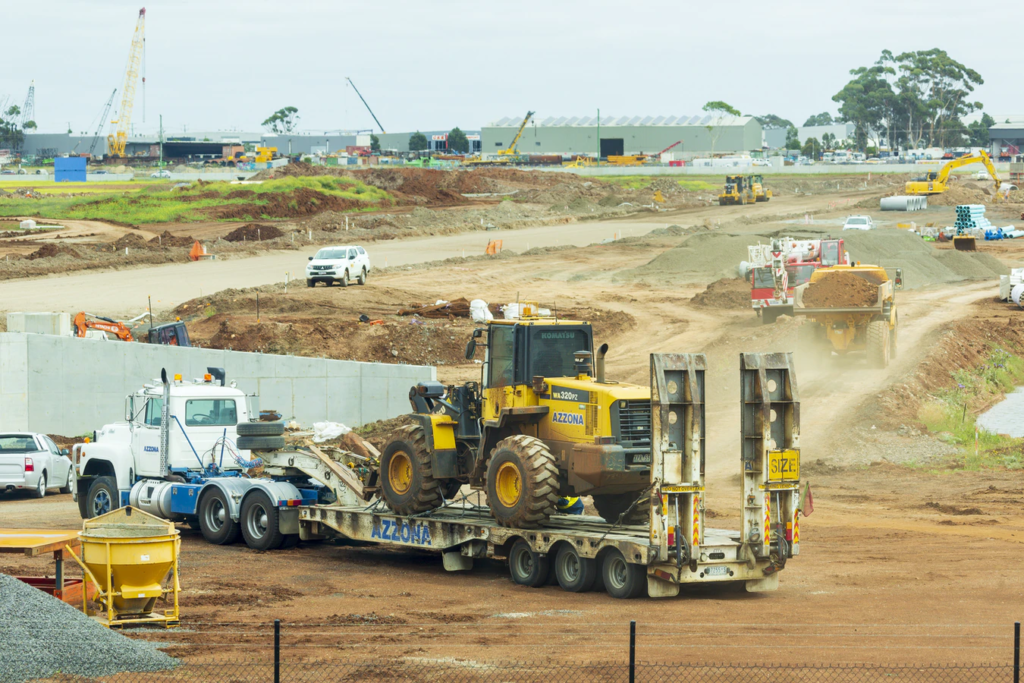
Establish a schedule — and stick to it: There are several factors throughout construction projects that could potentially delay the timeline and skyrocket costs for all parties involved. Not only can schedules offer a blueprint for success, but they can also offer transparency so everyone involved can easily track progress and identify areas for improvement.
Communication is key: Even with planning and scheduling, regular communication is crucial for avoiding costly delays or downtime. Before problems arise, develop a chain of command and protocol for addressing situations. Establish best practices for which conversations should happen in text or email, and which require in-person meetings or phone calls.
Put out one fire at a time: With so many moving parts and team members involved, it’s easy to get overwhelmed by the number of issues that need your attention. Part of your role as a project manager is to be a part-time firefighter, but even they have finite resources and must prioritize which blaze to tackle first.
Call in the pros: Sometimes a project is just too large or complex for one project manager to handle alone. This is the time to partner with a solutions provider that can find opportunities to fill in gaps. Construction project management professionals with the experience and expertise needed to support your work can help make your approach seamless and successful.
Construction scheduling project management is a critical piece of estimating the equipment costs for any major project. A realistic, logical calculation of the best-case scenarios, likely scenarios, and worst-case scenarios gives you and the project team an accurate schedule to work by. Delays are mitigated or avoided by accurate project planning and management of various construction time windows. With an expert on the ground, your project moves as seamlessly as possible through all stages of development —
let our team help.